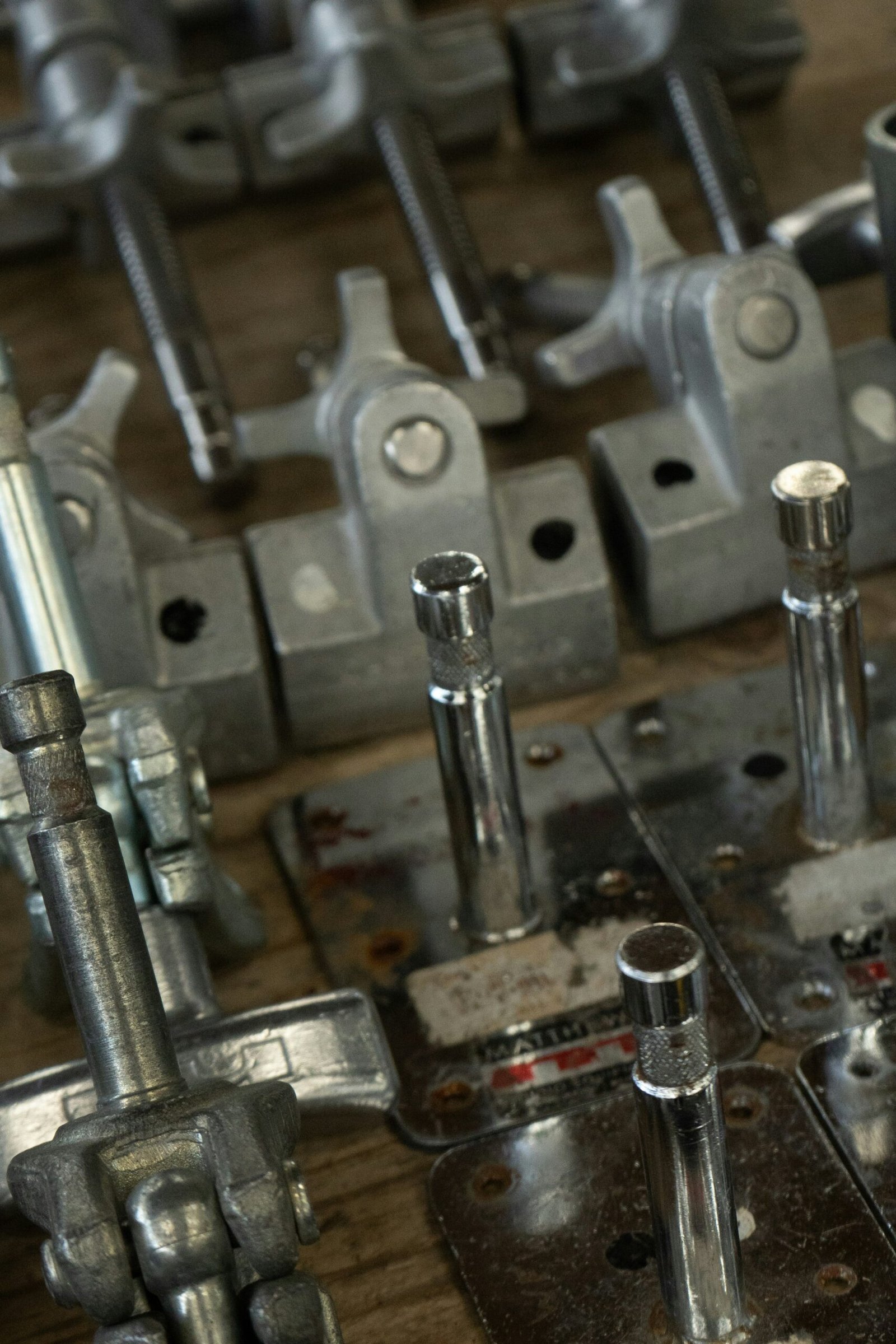
Introduction to Augmented Reality (AR) in Industrial Maintenance
Augmented Reality (AR) is a technology that superimposes digital information onto the real world, thereby enhancing users’ perception and interaction with their surroundings. In the realm of industrial maintenance, AR is revolutionizing the way maintenance tasks are executed. By integrating AR with existing technologies such as IoT (Internet of Things), AI (Artificial Intelligence), and advanced sensors, industries can gain real-time insights and actionable data directly within their field of view.
AR applications in industrial maintenance include overlaying instructions, highlighting critical components, and providing diagnostic information in real-time. This fusion of physical and digital realms facilitates a more intuitive and efficient approach to conducting maintenance tasks. The use of AR can significantly reduce downtime, improve accuracy, and enhance overall productivity by enabling maintenance personnel to perform their duties with greater precision and less reliance on traditional manuals or external guidance.
Several case studies underscore the increasing adoption of AR in various industries. For instance, a report by PTC highlighted that companies deploying AR for maintenance experienced a 30% reduction in operational costs and a 25% decrease in repair times. Similarly, Boeing reported a 40% improvement in productivity when employing AR for complex wiring tasks in aircraft manufacturing. These statistics illustrate the profound impact of AR in enhancing operational efficiency and cost savings.
Moreover, the global AR market in industrial sectors is projected to grow significantly. According to MarketsandMarkets, the AR market size is expected to reach USD 72.7 billion by 2026, with a compound annual growth rate (CAGR) of 46.6% from 2021 to 2026. This growth is driven by the increasing demand for AR-based training and maintenance solutions, as they offer compelling advantages like real-time remote assistance, streamlined workflows, and enhanced safety measures.
In essence, the integration of Augmented Reality into industrial maintenance practices is not just a trend but a transformative shift that promises substantial benefits. Its adoption is paving the way for smarter, faster, and more reliable maintenance operations.
Key Benefits of AR in Industrial Maintenance
Augmented Reality (AR) stands as a transformative technology in the realm of industrial maintenance. One of its primary benefits is the significant improvement in efficiency. By overlaying digital information onto physical equipment, maintenance teams can quickly identify and diagnose issues, reducing the time spent on troubleshooting. This immediacy in problem-solving translates directly into reduced downtime, ensuring that production lines remain operational and productive.
Another critical advantage of AR is the enhancement of safety protocols. Maintenance personnel often operate in hazardous environments where the margin for error is minimal. AR can offer real-time guidance and visual cues, helping workers to follow safety procedures meticulously. For instance, AR can project step-by-step instructions onto machinery, guiding technicians through complex repair processes without needing to refer to manuals or external devices.
Moreover, AR’s capacity to provide real-time information is invaluable. Maintenance teams can access up-to-date data on equipment status, performance metrics, and historical maintenance records, all through AR interfaces. This immediate access to comprehensive information helps in making informed decisions swiftly, thereby optimizing the maintenance workflow.
A practical application of AR in industrial maintenance is remote assistance. Experts located off-site can use AR to virtually “see” the problem through the eyes of the on-site technician. They can then offer precise guidance, reducing the need for travel and allowing for more rapid resolution of issues. This capability is particularly beneficial in geographically dispersed operations where specialist knowledge may not be readily available on-site.
Training and skill development also see substantial improvements with AR. New employees can engage with interactive, AR-based training modules that simulate real-life scenarios. This hands-on approach accelerates the learning curve and ensures that personnel are well-prepared to handle actual maintenance tasks.
Lastly, the visualization of complex systems through AR enables technicians to understand intricate machinery and processes better. By visualizing the internal workings of equipment, maintenance personnel can perform more accurate diagnostics and repairs, further enhancing the overall efficiency and reliability of industrial operations.
Challenges and Solutions in Implementing AR for Industrial Maintenance
Implementing Augmented Reality (AR) in industrial maintenance comes with its own set of challenges. One of the primary concerns for many industries is the initial investment cost. The expense of acquiring AR hardware, software, and related infrastructure can be significant. Additionally, the maintenance and updates required for these technologies add to the overall cost. Nevertheless, the long-term benefits of AR, such as improved efficiency and reduced downtime, often justify this investment.
Another critical challenge is the technical difficulties associated with integrating AR into existing systems. Industrial operations often rely on legacy systems that may not be compatible with modern AR solutions. This necessitates extensive modifications or even a complete overhaul of current systems, which can be both time-consuming and costly. To mitigate these issues, it is essential to choose AR solutions that are adaptable and can be seamlessly integrated with existing infrastructure.
Resistance to change from workers is another obstacle industries face when adopting AR technology. Employees accustomed to traditional maintenance methods might be hesitant to embrace new technologies. This resistance can stem from a lack of understanding or fear of job displacement. To address this, industries should invest in comprehensive training programs. These programs should educate workers about the advantages of AR and provide hands-on experience with the technology, thereby easing the transition.
Moreover, a gradual implementation strategy can be an effective solution to these challenges. Instead of a wholesale change, industries can introduce AR in phases, starting with pilot projects in specific areas. This approach allows them to evaluate the technology’s impact, make necessary adjustments, and gradually expand its usage.
Finally, selecting the right AR solution tailored to specific industrial needs is crucial. Not all AR technologies are created equal, and what works for one industry may not be suitable for another. Conducting thorough research and consulting with experts can help in choosing an appropriate AR system that aligns with the unique requirements and constraints of the industry.
Future Trends and Innovations in AR for Industrial Maintenance
As technology continues to advance at an unprecedented pace, the future of Augmented Reality (AR) in industrial maintenance looks promising. One of the key advancements anticipated is the improvement in AR hardware. Devices such as AR glasses and headsets are expected to become more ergonomic, offering enhanced comfort and usability for extended periods. This will facilitate hands-free operation, allowing technicians to access critical information and instructions without interrupting their workflow.
AR’s integration with Artificial Intelligence (AI) is another significant trend on the horizon. AI algorithms can analyze data in real-time, providing predictive maintenance insights and identifying potential issues before they escalate into major problems. By combining AR with AI, maintenance systems can offer more precise diagnostics and tailored troubleshooting guidance, thereby improving efficiency and reducing downtime.
In addition to hardware and AI advancements, software innovations are also set to play a crucial role in the evolution of AR for industrial maintenance. Enhanced software solutions will offer more intuitive interfaces, enabling users to interact seamlessly with virtual overlays. These software improvements will also facilitate better data management and analytics, providing actionable insights that can optimize maintenance schedules and resource allocation.
Looking ahead, the potential impact of AR on industrial maintenance is immense. Predictive maintenance powered by AR and AI could become the norm, significantly reducing unexpected equipment failures and associated costs. Furthermore, the adoption of 5G technology will enable faster and more reliable data transmission, ensuring real-time updates and collaboration, even in remote locations.
Emerging innovations such as holographic displays and multi-user AR experiences could revolutionize the field. Holographic displays would allow maintenance teams to visualize complex components in three dimensions, facilitating a deeper understanding and more accurate repairs. Multi-user AR experiences would enable collaborative troubleshooting, with experts from different locations working together in a shared virtual space.