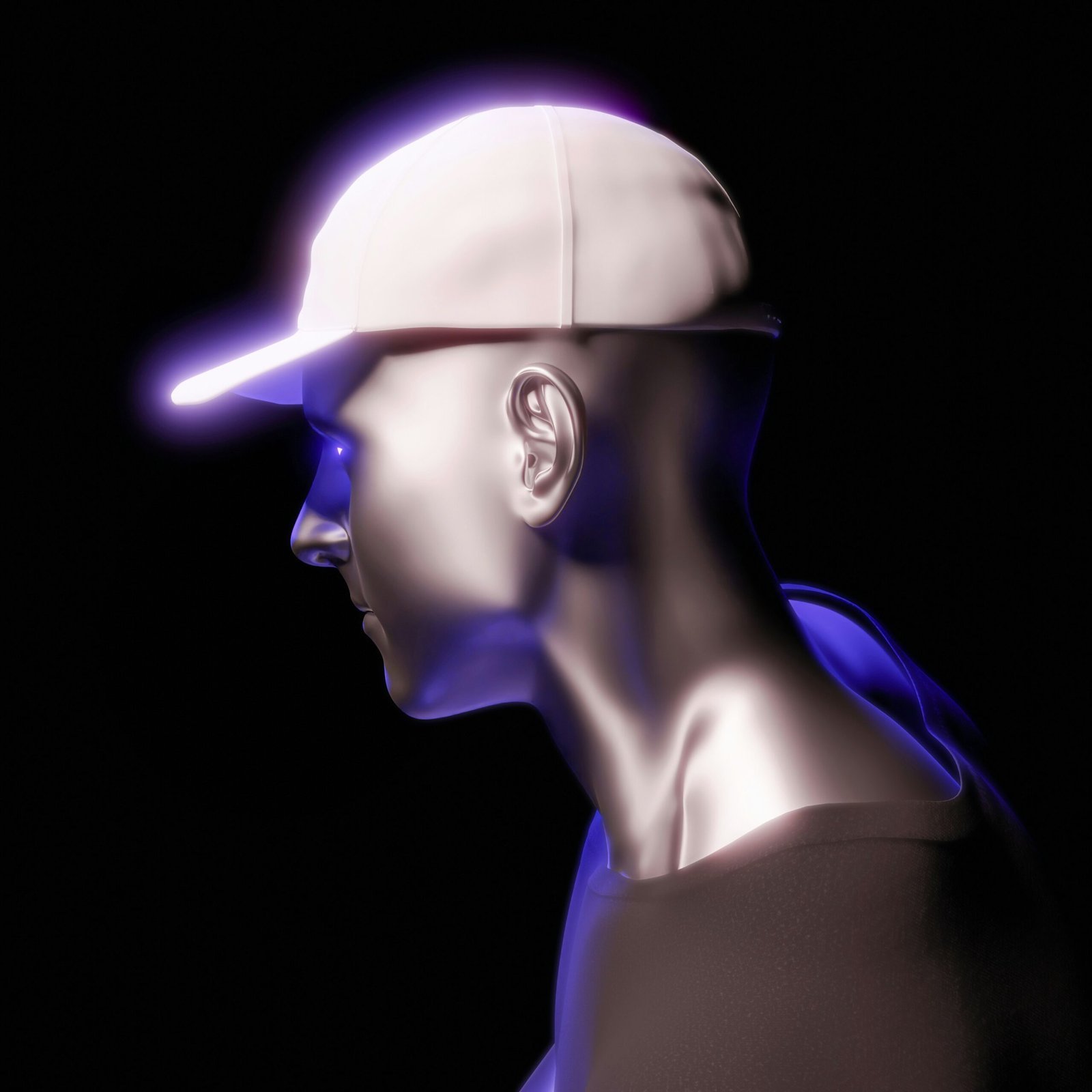
Introduction to 3D Printing and Supply Chain Management
3D printing, also known as additive manufacturing, has evolved considerably since its inception in the 1980s. Initially used for prototyping, this innovative technology has now expanded its reach into various industries, from healthcare to aerospace, through advancements that allow for the creation of both simple and complex structures. The ability to produce customized and intricate designs with a high degree of accuracy has positioned 3D printing as a transformative force in manufacturing and beyond.
In parallel, supply chain management (SCM) encompasses the planning, implementation, and supervision of a range of activities involved in producing goods and services. A well-managed supply chain is crucial to a company’s success, as it ensures the efficient flow of information, materials, and products from suppliers to manufacturers and finally to consumers. In today’s fast-paced global economy, optimizing supply chain processes is paramount for maintaining competitive advantage and customer satisfaction.
The intersection of 3D printing and SCM provides a fertile ground for innovation. 3D printing offers unprecedented flexibility in production, allowing companies to reduce lead times, minimize inventory, and respond more swiftly to market demands. This agility aligns seamlessly with the objectives of supply chain management, which seeks to streamline operations and enhance responsiveness.
As we delve deeper into this discussion, it is crucial to understand how 3D printing can revolutionize traditional supply chain processes. For example, localized production enabled by 3D printing can diminish reliance on distant suppliers and reduce transportation costs. Furthermore, the capability to produce customized parts on-demand can significantly decrease the need for large stockpiles, thereby reducing storage costs and waste.
In essence, 3D printing holds the promise of a more nimble, efficient, and cost-effective supply chain. By integrating this technology, businesses have the opportunity to reimagine and enhance their supply chain strategies, ensuring they are well-positioned to thrive in a dynamic market landscape.
Advantages of 3D Printing in Supply Chain Management
3D printing, also known as additive manufacturing, offers a multitude of advantages for supply chain management. One of the most significant benefits is the reduction in lead times. Traditional manufacturing often involves lengthy processes, including prototyping, tooling, and production runs. In contrast, 3D printing can swiftly create prototypes and final products directly from digital designs, cutting down lead times significantly. For instance, companies like General Electric have leveraged 3D printing to produce complex aircraft components in a fraction of the usual time, allowing for quicker market entry and iterative improvements.
Another substantial advantage is the reduction of inventory costs. With the ability to print parts on-demand, businesses can minimize their need for large inventories. This just-in-time manufacturing approach reduces warehousing costs and mitigates the risk of overproduction. A relevant example is Siemens, which uses 3D printing to produce spare parts for its trains and industrial turbines, maintaining production efficiency while significantly reducing inventory obligations.
3D printing also enhances customization and flexibility in production. Traditional manufacturing often requires dedicated tooling and molds for each unique product, which can be prohibitively expensive for small batches or customized items. In contrast, 3D printing allows for easy customization without additional tooling costs. The healthcare industry, for example, benefits immensely from this capability, as companies like Align Technology use 3D printing to create custom dental aligners tailored to each patient’s unique dental structure.
Lastly, the potential for decentralizing production is another significant advantage. 3D printing enables production to be closer to the point of consumption, reducing transportation costs and mitigating supply chain disruptions. This decentralization has been particularly beneficial in remote or resource-limited areas. Moreover, companies like Adidas have adopted this approach by establishing local production facilities equipped with 3D printers to produce customized footwear, thus enhancing responsiveness to market demands and reducing logistical complexities.
Challenges and Limitations of Implementing 3D Printing in Supply Chains
While the adoption of 3D printing technology in supply chains presents notable advantages, several challenges and limitations persist. Chief among these challenges is the high cost of 3D printing equipment and materials. The initial investments required for cutting-edge 3D printers can be prohibitive for many businesses, particularly small and medium-sized enterprises. Additionally, the specialized materials needed for high-quality and precise prints come at a premium, significantly impacting cost-effectiveness.
Another substantial concern is quality control. In traditional manufacturing, rigorous quality control processes are well-established. However, ensuring consistency and reliability in 3D printed products poses difficulties. Variations in material properties, printer calibration, and operator skill can introduce inconsistencies, complicating the maintenance of high standards. To mitigate these issues, robust quality assurance protocols and thorough testing mechanisms must be developed and refined.
Intellectual property (IP) risks also present significant hurdles in the integration of 3D printing into supply chains. The digital nature of 3D design files makes them vulnerable to unauthorized replication and distribution. Businesses face the challenge of securing their proprietary designs and preventing infringement, which can be a daunting task given the ease with which digital files can be shared. Developing stringent IP protection strategies and leveraging advanced cybersecurity measures are critical in addressing these concerns.
Regulatory hurdles add an additional layer of complexity. As 3D printing technology continues to evolve, regulatory frameworks struggle to keep pace. This lag creates uncertainty around compliance, particularly in highly regulated industries such as aerospace, medical devices, and automotive manufacturing. Navigating these evolving regulations requires businesses to be proactive in understanding and aligning with current and future standards.
In summary, while 3D printing offers transformative potential for supply chains, significant challenges and limitations must be tackled. Addressing the high costs, ensuring quality control, protecting intellectual property, and navigating regulatory complexities are essential steps for successful integration of 3D printing into existing supply chain systems.
Future Trends and Potential of 3D Printing in Supply Chain Management
As 3D printing continues to evolve, it stands poised to redefine the contours of supply chain management. Among the most anticipated trends is the significant advancement in the materials used for 3D printing. Innovations in biocompatible materials, high-strength polymers, and metal alloys are expected to expand the application spectrum, enabling production of more complex and durable components with precision.
The growth of distributed manufacturing is another promising trend, where small-scale, localized production units can leverage 3D printing to fulfill specific regional demands. This evolution will likely diminish dependency on centralized manufacturing hubs, thus reducing lead times and transportation costs. Consequently, companies can maintain lower inventory levels, streamline logistics, and enhance their environmental sustainability by minimizing the carbon footprint associated with long-distance shipping.
Furthermore, the integration of 3D printing into supply chain strategies is expected to shift from a niche application to a mainstream practice. Businesses are increasingly recognizing the strategic advantages of additive manufacturing, such as the ability to swiftly prototype, customize products at scale, and produce on-demand spare parts, thereby mitigating supply chain disruptions. Advanced data analytics and IoT will further enhance the efficiency of these processes, enabling seamless coordination between design, production, and distribution stages.
Potential industry disruptions could arise, with certain sectors experiencing more profound transformations than others. For instance, the aerospace and healthcare industries are likely to benefit substantially from the precise and customizable nature of 3D printing, potentially revolutionizing aircraft part production and bespoke medical devices. On the other hand, traditional manufacturing sectors may need to adapt swiftly to remain competitive in an increasingly additive-controlled environment.
The long-term potential of 3D printing in supply chain management is vast and inspiring. As the technology matures, stakeholders must remain vigilant, adaptable, and innovative to harness its full capabilities. By proactively integrating 3D printing into their supply chain strategies, businesses can unlock significant efficiencies, drive growth, and stay ahead of the curve in the face of upcoming changes.