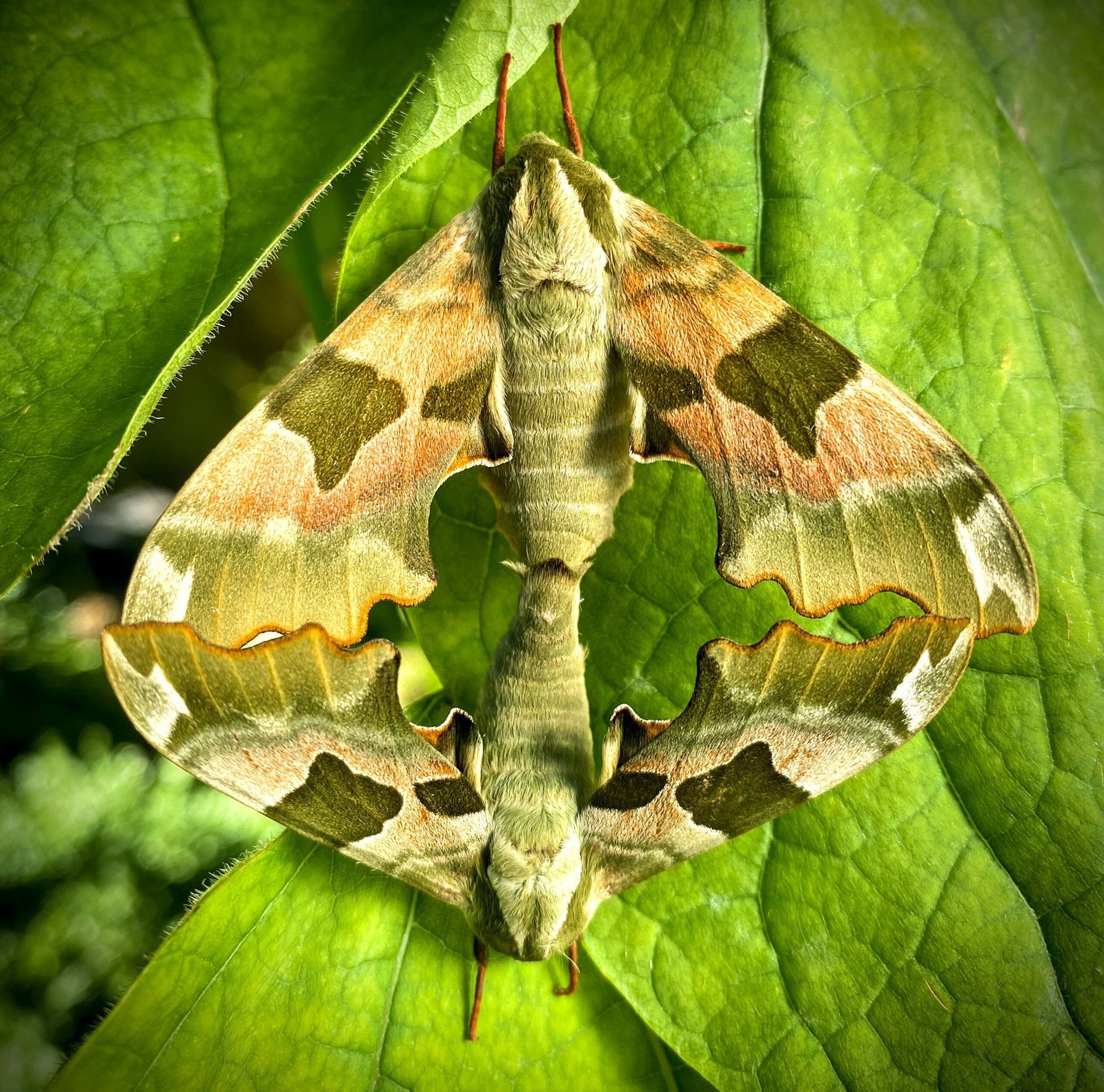
Introduction to Digital Twins in Manufacturing
Digital twins are emerging as a transformative technology in the manufacturing industry, poised to optimize production processes and enhance operational efficiency. A digital twin can be defined as a virtual replica of a physical asset, system, or process. This digital counterpart is created and maintained through a combination of advanced technologies, including the Internet of Things (IoT), artificial intelligence (AI), and big data analytics.
At its core, the concept of a digital twin involves capturing real-time data from sensors and other data collection tools installed on physical manufacturing assets. This data is then processed and analyzed using AI algorithms to create a dynamic, real-time digital model of the physical asset. The digital twin continuously updates and evolves in sync with its physical counterpart, enabling manufacturers to monitor, analyze, and optimize their operations remotely and in real time.
The foundational technology driving digital twins includes IoT, which plays a critical role in connecting physical devices and systems to the digital realm. Sensors embedded in machinery and equipment collect voluminous data on various parameters—ranging from temperature and pressure to vibration and operational status. This data serves as the lifeblood of the digital twin, providing the essential input needed to create an accurate and functional virtual model.
AI enhances digital twins by providing sophisticated analytical capabilities that can predict equipment failure, recommend optimization strategies, and simulate different manufacturing scenarios. By leveraging machine learning algorithms, digital twins can provide insights that go beyond simple monitoring, offering predictive maintenance and decision-making support that significantly enhance operational efficiency.
Big data analytics is indispensable to the functioning of digital twins, as it processes the massive volume of data generated by IoT devices. The ability to analyze this data in real time allows manufacturers to derive actionable insights, improve predictive maintenance, and optimize production schedules.
As the manufacturing industry becomes increasingly competitive and complex, digital twins offer a powerful tool for achieving greater efficiency, enhancing production quality, and reducing operational costs. By providing a holistic, real-time view of manufacturing assets and processes, digital twins are revolutionizing how manufacturers monitor, manage, and optimize their operations.
The Benefits of Implementing Digital Twins in Production
Digital twins have emerged as a transformative technology in the manufacturing sector, offering several compelling advantages that streamline production processes. One of the primary benefits is enhanced operational efficiency. By creating a virtual model that mirrors the physical production environment, manufacturers can simulate different scenarios and identify potential bottlenecks. This proactive analysis enables optimization of processes, reducing waste and improving throughput.
Predictive maintenance is another key advantage of digital twins. Traditional maintenance schedules often result in excessive downtime and unnecessary costs. In contrast, a digital twin allows for continuous monitoring of machinery and equipment health in real-time. By leveraging advanced analytics and machine learning algorithms, it is possible to predict when a machine is likely to fail and take preventative measures. This approach mitigates unplanned downtime, extends asset lifespan, and leads to significant cost savings.
Real-time monitoring is integral to the efficacy of digital twins. Operators receive instantaneous feedback from the digital replica, allowing for timely interventions and adjustments. This continuous data flow enhances visibility into the production floor, enabling swift and informed decision-making. It also fosters a more responsive manufacturing environment where issues can be addressed before escalating into more significant problems.
Digital twins also contribute to improved product quality. As processes are optimized and machinery maintenance becomes more predictive, the consistency of production quality increases. Real-time data can be used to fine-tune manufacturing parameters, ensuring products meet exact specifications. Consequently, manufacturers achieve higher quality standards and customer satisfaction.
Several companies have already successfully integrated digital twins into their production processes, reaping considerable benefits. For example, a leading aerospace manufacturer utilized digital twins to simulate and optimize assembly line operations. This initiative led to a 15% increase in production efficiency and considerable cost savings. Similarly, an automotive company used digital twins for real-time monitoring and predictive maintenance, resulting in a 20% reduction in downtime and increased overall equipment effectiveness.
In summary, digital twins offer multifaceted benefits to the manufacturing industry, including enhanced efficiency, predictive maintenance, real-time monitoring, and improved product quality. Through practical case studies, the tangible advantages of implementing digital twins are evident, showcasing their value in optimizing production processes.
Key Technologies and Data Integration
Digital twins in manufacturing are powered by a convergence of advanced technologies, each playing a crucial role in optimizing production processes. At the forefront are sensors, which are essential for collecting real-time data from physical assets. These sensors capture a plethora of information, including temperature, pressure, and vibration, providing a granular view of the manufacturing environment. The integration of this sensor data is paramount for creating an accurate and functional digital twin.
Data analytics is another cornerstone technology, transforming raw data into meaningful insights. By applying sophisticated analytical methodologies, manufacturers can identify patterns, predict failures, and optimize production schedules. These analytical processes are greatly enhanced by the capabilities of cloud computing. Cloud platforms offer scalable storage and computational power necessary to handle vast amounts of data generated by manufacturing operations. This scalability ensures that digital twins can grow in complexity without being hampered by hardware limitations.
Edge computing complements cloud resources by bringing data processing closer to the source of data generation. This proximity reduces latency and allows for real-time insights and actions, crucial for maintaining the efficiency and responsiveness of manufacturing systems. The blend of cloud and edge computing creates a robust infrastructure that supports the dynamic nature of digital twins.
Machine learning algorithms play an indispensable role in extracting actionable insights from large datasets. By learning from historical and real-time data, these algorithms can predict equipment failures, suggest maintenance schedules, and optimize production parameters, thereby enhancing overall productivity. However, the efficacy of these algorithms is heavily reliant on data quality and integration. Ensuring high-quality, consistent, and well-integrated data streams is essential for deriving accurate and valuable insights.
Implementing these technologies, however, comes with challenges. Cybersecurity concerns are prevalent, as the integration of numerous IoT devices and cloud services increases the number of potential entry points for cyberattacks. To mitigate these risks, manufacturers must invest in robust cybersecurity measures and adopt best practices such as encryption, regular security audits, and network segmentation.
Data privacy is another significant issue, particularly when dealing with sensitive information. Compliance with regulations such as GDPR and CCPA is imperative to avoid legal repercussions and maintain customer trust. Establishing clear data governance policies and leveraging anonymization techniques can help address these privacy concerns effectively.
Future Trends and Implications for Manufacturing
The evolution of digital twin technology is tightly interwoven with advancements in artificial intelligence (AI) and machine learning (ML). As these technologies continue to mature, the integration of AI and ML with digital twins holds the promise of more sophisticated, self-optimizing systems that can predict and prevent issues before they arise. This predictive capability will be instrumental in minimizing downtime, enhancing efficiency, and reducing costs in manufacturing processes.
In the context of Industry 4.0, digital twins are becoming increasingly pivotal. They offer a bridge between the physical and digital worlds, enabling manufacturers to achieve unprecedented levels of insight and control. By simulating real-world scenarios, digital twins allow for more agile and responsive manufacturing operations, where adjustments can be made in real-time to optimize performance and adapt to changing conditions. This agility is crucial for manufacturers aiming to remain competitive in a rapidly evolving marketplace.
Moreover, digital twins are poised to revolutionize supply chain optimization. By creating dynamic models of supply chains, manufacturers can gain a granular understanding of how different variables impact the entire network. This insight facilitates more informed decision-making, leading to improved resource allocation, reduced lead times, and enhanced overall efficiency. The ability to simulate and optimize supply chain processes in this manner represents a significant advancement over traditional approaches.
Smart factories stand to benefit immensely from the continuous development of digital twins. In these highly automated environments, digital twins can monitor equipment conditions, optimize production schedules, and even coordinate the actions of interconnected systems. This holistic approach to management not only boosts productivity but also ensures higher quality outputs by mitigating risks and reducing the likelihood of errors.
Looking ahead, the implications of digital twins for the manufacturing landscape are profound. As the technology evolves, it will not only redefine operational paradigms but also drive innovation in ways we have yet to fully envision. Manufacturers who embrace digital twins will be well-positioned to lead in an era of smarter, more efficient production processes, ultimately reshaping the industry and setting new standards for excellence.