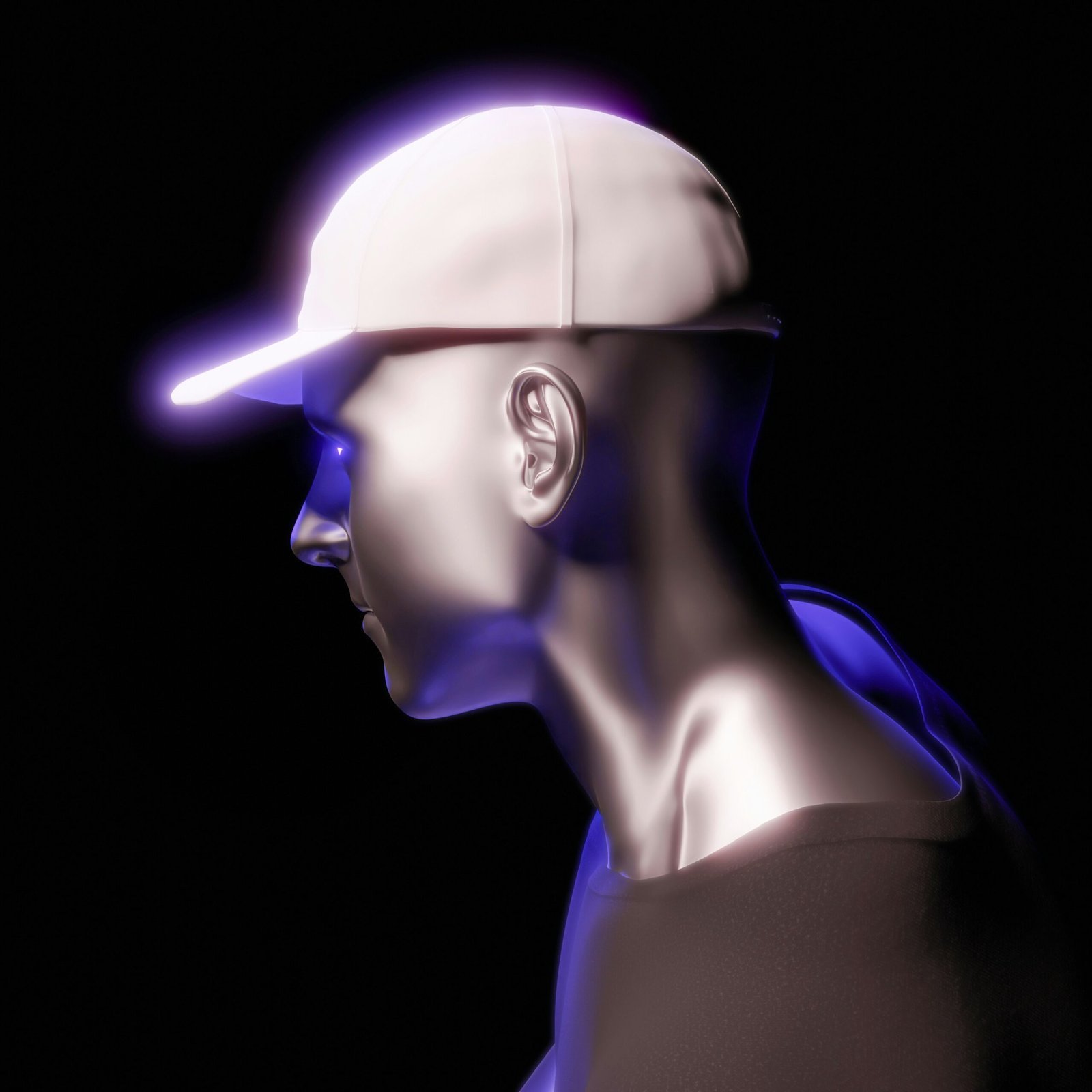
Introduction to 3D Printing and Rapid Prototyping
3D printing, also known as additive manufacturing, has emerged as a groundbreaking technology in the manufacturing sector. By building objects layer by layer from digital models, 3D printing has revolutionized the way products are developed and produced. This technology is particularly significant in the realm of rapid prototyping, which involves the quick fabrication of a scale model of a physical part or assembly using three-dimensional computer-aided design data.
The concept of rapid prototyping dates back to the 1980s, with the advent of technologies such as stereolithography (SLA) developed by 3D Systems. This marked the beginning of a transformative journey for manufacturing processes. Subsequent advancements have seen the introduction of techniques like fused deposition modeling (FDM) and selective laser sintering (SLS), which have further expanded the capabilities and applications of 3D printing.
In the context of rapid prototyping, 3D printing offers several key advantages. It significantly reduces product development cycles by enabling quick iterations and modifications. Traditional prototyping methods often involve lengthy and costly tooling processes, whereas 3D printing allows for rapid production of prototypes, facilitating faster decision-making and iteration. This accelerated pace not only decreases time-to-market but also fosters innovation by enabling designers and engineers to experiment and refine their ideas with greater flexibility and less financial risk.
Moreover, 3D printing supports a wide range of materials, from plastics to metals, which further enhances its utility in producing functional prototypes that closely resemble the final product. This capability is crucial for testing the form, fit, and function of new designs before committing to full-scale production.
The evolution of 3D printing technology has also seen significant milestones, including the development of multi-material and bioprinting technologies. These advancements have opened new possibilities in industries such as healthcare, aerospace, and automotive manufacturing, where precision and customization are paramount.
To sum up, 3D printing has fundamentally transformed rapid prototyping, making it an indispensable tool in modern manufacturing. Its ability to streamline the product development process, reduce costs, and promote innovation underscores its growing importance in the industry.
Benefits of 3D Printing in Rapid Prototyping
3D printing has revolutionized rapid prototyping by providing a cost-effective, swift, and versatile solution to traditional manufacturing methods. One of the most significant advantages is the reduction in production costs. Traditional prototyping often involves expensive tooling and labor-intensive processes, whereas 3D printing eliminates these costs by using additive manufacturing techniques. This cost-effectiveness allows for financial flexibility and resource allocation to other critical areas of product development.
Speed is another critical benefit of 3D printing in rapid prototyping. Traditional methods can take weeks or even months to produce a prototype, while 3D printing can accomplish this within days or even hours. This rapid turnaround accelerates the product development cycle, enabling businesses to bring their products to market faster and respond more swiftly to market demands.
The ability to create complex geometries is a unique advantage of 3D printing. Traditional manufacturing methods often struggle with intricate designs that require multiple components and assembly processes. In contrast, 3D printing can produce highly complex, single-piece structures that would be impossible or prohibitively expensive to manufacture traditionally. This capability is particularly beneficial in industries like aerospace and automotive, where lightweight and complex designs are crucial for performance and efficiency.
Industries such as healthcare, consumer electronics, and automotive have significantly benefited from these advantages. For instance, in the healthcare sector, 3D printing enables the creation of customized prosthetics and implants tailored to individual patients’ needs. In the automotive industry, manufacturers can rapidly prototype and test new parts, leading to more innovative and efficient vehicle designs. Consumer electronics companies leverage 3D printing to develop intricate components for devices, enhancing functionality and user experience.
Furthermore, 3D printing facilitates more iterative design processes. Designers and engineers can quickly produce multiple prototype versions, test them, and refine their designs based on feedback. This iterative approach leads to higher-quality products and reduces the risks associated with design flaws. Enhanced customization is another significant benefit, allowing businesses to tailor products to specific customer requirements, thereby providing a competitive edge in the market.
Challenges and Limitations of 3D Printing in Rapid Prototyping
The utilization of 3D printing in rapid prototyping has transformed manufacturing processes; however, it is not devoid of challenges and limitations. One of the primary issues is the material limitations associated with 3D printing. While traditional manufacturing allows for a variety of materials such as metals, plastics, and composites, 3D printing is currently more restricted. The range of materials available for 3D printing, although expanding, does not yet match the extensive options provided by conventional manufacturing techniques. This limitation can hinder the ability to prototype using the exact materials intended for the final product.
Another significant challenge is the current state of 3D printing technology. Despite advancements, 3D printers, especially at the consumer level, often lack the precision and reliability required for intricate and highly detailed prototypes. High-end 3D printers that offer superior accuracy and capabilities come with a substantial cost, making them less accessible for small businesses and individual creators. Furthermore, these advanced machines necessitate a specialized skill set to operate effectively. Mastery in software usage, machine calibration, and troubleshooting are crucial, placing a high demand on the operator’s expertise.
Post-processing requirements also present a noteworthy limitation. Many 3D printed objects require additional finishing steps such as sanding, painting, or chemical treatments to meet the desired quality and functionality. This need for post-processing can extend the prototyping timeline and add to the overall cost, diminishing some of the speed advantages that 3D printing initially offers.
Intellectual property (IP) concerns are another aspect that impacts the rapid prototyping process. The ease with which digital files can be replicated raises significant issues regarding the protection of designs and proprietary technology. Unauthorized copying and distribution of 3D printed designs can lead to IP infringements, posing a substantial risk to inventors and companies alike.
Future Trends and Innovations in 3D Printing for Rapid Prototyping
The future of 3D printing in rapid prototyping is set to be transformative, driven by cutting-edge technologies and innovative materials designed to overcome existing limitations. One of the most promising advancements lies in the development of faster printing processes. Emerging technologies such as continuous liquid interface production (CLIP) and Multi Jet Fusion (MJF) are poised to substantially reduce print times while enhancing the precision and quality of prototypes. These advancements promise to streamline product development cycles, allowing manufacturers to iterate and refine designs more efficiently than ever before.
Moreover, the capability to print with multiple materials simultaneously is becoming increasingly attainable. This development is crucial for creating functional prototypes that closely mimic final products, incorporating various mechanical, thermal, and electrical properties. Innovations in both hardware and software are enabling more complex and multi-material prints, providing comprehensive solutions for industries ranging from healthcare to automotive.
Artificial intelligence (AI) and machine learning (ML) are also set to play a pivotal role in the future of 3D printing. These technologies can optimize printing processes by predicting potential failures, adjusting parameters in real-time, and ensuring consistent quality. AI-driven design tools can generate more efficient geometries and support structures, reducing material waste and print times. Machine learning algorithms can analyze vast amounts of data from previous prints to continually improve the accuracy and efficiency of new prints, making the entire process more reliable and cost-effective.
Furthermore, the development of new materials, including advanced polymers, metals, and biocompatible substances, will expand the applicability of 3D printing. These materials will allow for the creation of prototypes that are not only more durable but also capable of performing under specific conditions, thereby providing a more accurate representation of the final product.
In conclusion, the rapid evolution of 3D printing technologies, combined with advancements in AI and material science, is poised to revolutionize rapid prototyping. These innovations will significantly shorten product development cycles and broaden the scope of rapid prototyping, making it an indispensable tool across various industries.