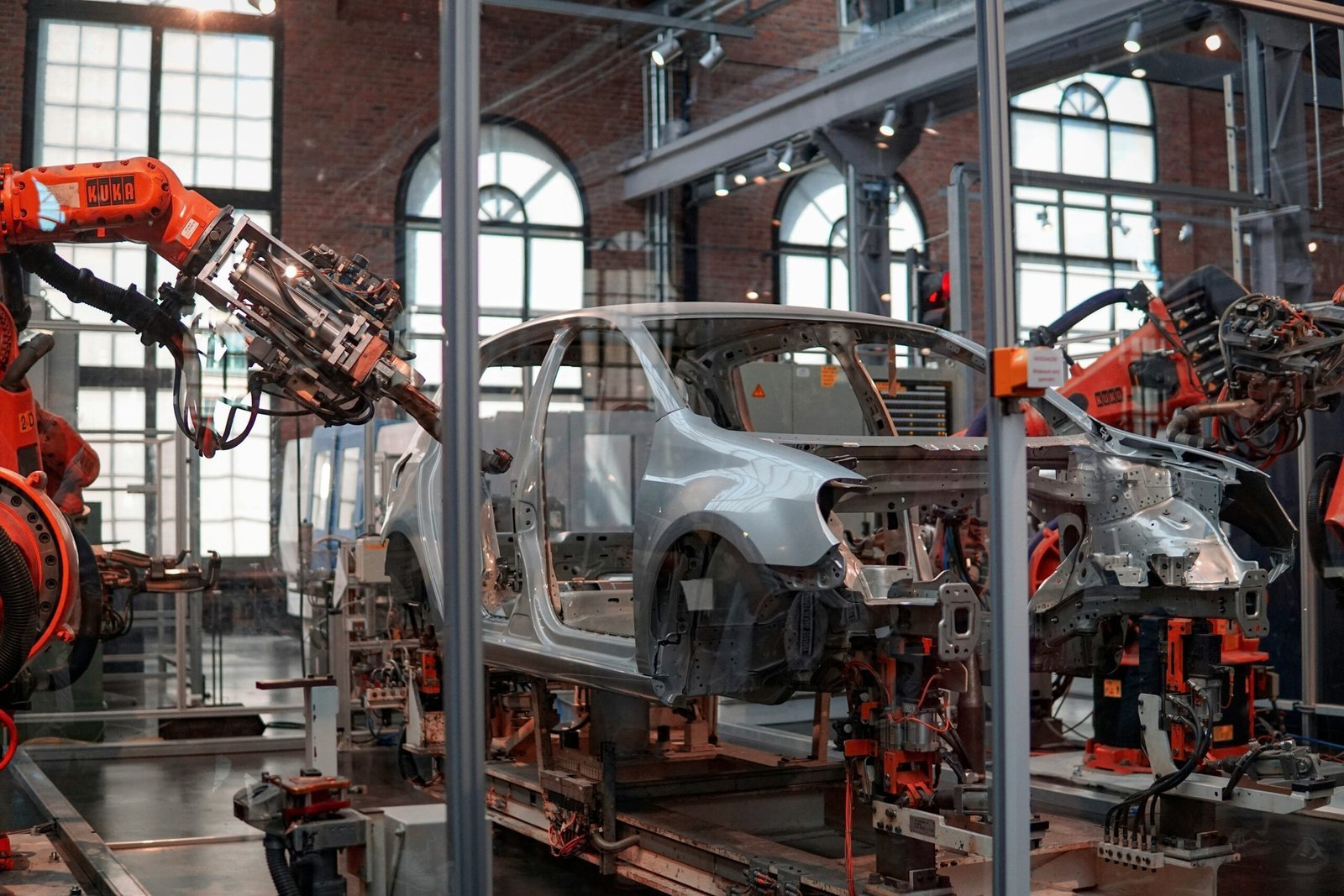
Introduction to Robotics in Manufacturing
The integration of robotics technology into the manufacturing sector has revolutionized the industry, marking a significant shift from traditional methods to advanced automated systems. Historically, the journey began in the mid-20th century with the advent of the first industrial robots, which were initially met with skepticism and cautious optimism. Early adopters faced numerous challenges, including high costs, technological limitations, and resistance from a workforce concerned about job displacement. Despite these hurdles, the potential benefits of enhanced efficiency, precision, and productivity drove continued experimentation and development.
Over time, the evolution of robotics in manufacturing saw the emergence of various types of robots, each designed to fulfill specific roles within the production process. Robotic arms, for instance, became common fixtures on assembly lines due to their ability to perform repetitive tasks with high accuracy and speed. Automated Guided Vehicles (AGVs) transformed material handling by autonomously navigating complex industrial environments to transport goods. Collaborative robots, or cobots, represent another significant advancement, allowing humans and robots to work side by side, thereby combining human creativity with robotic efficiency.
At the core of this revolution are the basic principles of robotic automation, which encompass the use of sensors, actuators, and control systems to enable machines to perform tasks independently. Advanced technologies such as machine learning and artificial intelligence have further enhanced these capabilities, allowing robots to adapt to new tasks and optimize their performance over time. The integration of robotics into manufacturing has not only improved operational efficiency but has also paved the way for innovations in product quality and customization.
While the initial adoption phase was fraught with challenges, the relentless pursuit of technological advancement has cemented robotics as an indispensable component of modern manufacturing. As the industry continues to evolve, the role of robotics is poised to expand even further, driving unprecedented levels of efficiency and innovation.
Enhancements in Production Efficiency
Robotics has revolutionized manufacturing by significantly enhancing production efficiency. One of the primary ways this has been achieved is through the unparalleled speed and precision that robotic systems offer. Unlike human workers, robots can perform tasks with a high degree of accuracy and consistency, thereby reducing errors and enhancing the quality of the final product. This precision is especially beneficial in industries requiring meticulous assembly or delicate handling of components, such as electronics and pharmaceuticals.
Another key advantage of robotics is the reduction of human error, which is inevitable in manual processes. Automated systems follow programmed instructions to the letter, ensuring that each product is manufactured to exact specifications. This not only improves product quality but also reduces waste, leading to cost savings and more efficient use of resources.
Moreover, robotic systems can operate continuously without fatigue, a significant limitation for human workers. This enables 24/7 production cycles, drastically increasing output and ensuring that manufacturing plants can meet high demand without compromising on quality or speed. The ability to handle complex and repetitive tasks without breaks further underscores the efficiency of robotic systems in manufacturing environments.
Real-world examples illustrate the transformative impact of robotics on manufacturing efficiency. For instance, automotive manufacturers like Ford and Toyota have integrated robotic arms for welding and assembly, leading to reduced cycle times and increased production volumes. Similarly, in the electronics sector, companies such as Foxconn have deployed robots for tasks like circuit board assembly, resulting in higher throughput and fewer defects.
In summary, the integration of robotics into manufacturing processes has led to significant enhancements in production efficiency. The speed, precision, and capability to operate continuously without fatigue make robots invaluable in modern manufacturing, driving improvements in productivity and output quality. These advancements underscore the essential role that robotics plays in the contemporary manufacturing landscape.
Impact on Workforce and Job Roles
The advent of robotics in the manufacturing sector has significantly influenced workforce dynamics and job roles. The integration of automated systems has led to a paradigm shift, raising concerns about job displacement. Indeed, automation has replaced many repetitive and labor-intensive tasks traditionally performed by human workers, leading to fears of widespread unemployment. However, this view overlooks the multifaceted impact of robotics on job roles and the overall labor market within the industry.
While it is undeniable that certain positions have become redundant due to automation, this technological advancement has also paved the way for the emergence of new job opportunities. Key areas such as robot maintenance, programming, and oversight have seen a notable increase in demand. These roles are essential for the smooth operation and continuous improvement of automated systems. Consequently, the workforce is witnessing a shift from manual labor to more specialized, technical positions that require a different set of skills.
The evolution of job roles necessitates a focus on upskilling and reskilling the existing workforce. Workers must be equipped with the knowledge and expertise needed to operate, maintain, and troubleshoot advanced robotic systems. This transition involves comprehensive training programs and educational initiatives aimed at bridging the skill gap. By investing in human capital, companies can ensure that their employees are not left behind in the rapidly changing landscape of manufacturing.
Moreover, the implementation of robotics has introduced a collaborative working environment where humans and robots coexist, often referred to as “cobots” – collaborative robots. These machines are designed to work alongside human workers, enhancing productivity while ensuring safety. This collaboration has redefined job roles, emphasizing the importance of human oversight and decision-making in conjunction with automated processes.
In conclusion, the impact of robotics on the manufacturing workforce is complex and multifaceted. Although automation has led to job displacement in certain areas, it has equally created new opportunities and necessitated the evolution of job roles. Through strategic upskilling and reskilling, the workforce can adapt and thrive in an industry increasingly dominated by robotics.
Future Trends and Innovations
As the landscape of manufacturing continues to evolve, the integration of advanced technologies into robotics promises to bring about significant enhancements in efficiency. One of the most noteworthy trends is the advancement of artificial intelligence (AI) and machine learning. These technologies enable robots to learn from their experiences and improve their performance over time. For instance, AI-driven robots can optimize production lines by predicting maintenance needs, reducing downtime, and adapting to new tasks with minimal human intervention.
Another key development is the rise of collaborative robots, or cobots. Unlike traditional industrial robots, which operate in isolation, cobots are designed to work alongside human workers. They are equipped with sensors and safety features that allow them to interact safely and effectively with people. Cobots can handle repetitive and strenuous tasks, thus enhancing worker productivity and reducing the likelihood of injury. The flexibility and ease of use that cobots bring to the table make them an attractive option for small and medium-sized enterprises (SMEs) seeking to automate their operations.
The integration of the Internet of Things (IoT) into robotic systems is also a game-changer for manufacturing efficiency. IoT-enabled robots can communicate with other devices and systems within a factory, creating a network of interconnected machines. This connectivity allows for real-time monitoring and data analysis, leading to more efficient and adaptive manufacturing processes. For example, IoT sensors can provide continuous feedback on the performance of robotic systems, enabling predictive maintenance and reducing the risk of unexpected breakdowns.
Looking ahead, the continuous advancements in robotic technology hold the potential to transform the manufacturing industry further. Emerging trends such as the development of autonomous mobile robots, which can navigate complex environments without human input, and the use of advanced materials for building more robust and versatile robots, are set to shape the future of manufacturing. As these innovations become more widespread, manufacturers can expect to see even greater improvements in efficiency, flexibility, and productivity.